
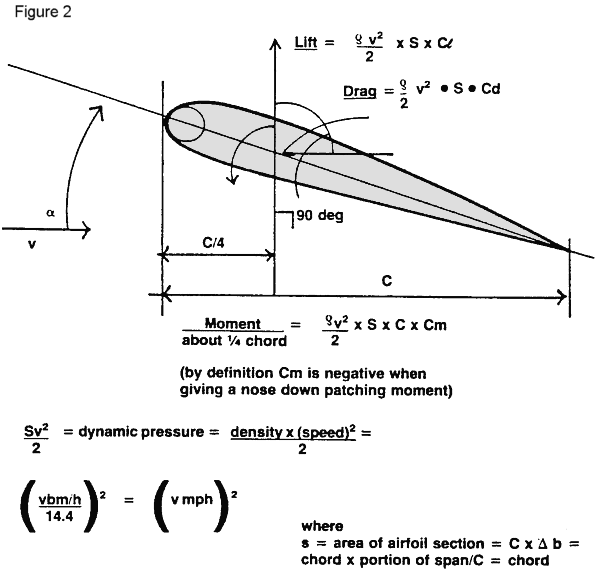
#High lift airfoil skin
Thrust exerted by the aircraft can create additional lift and drag due to skin friction along the surface of the craft, and particularly along the airfoil. Why Laminar Flow Over Airfoils?ĭuring flight, airflow across the wing of an aircraft creates drag and lift. We’ll discuss these aspects of laminar flow over airfoils and examine the limits of laminar flow across airfoils in this article. The reasons for this are varied, but they relate to the main aerodynamic forces acting on an aircraft, and particularly on the airfoil itself. Together, these are the main determining factors used to design aircraft to reach engineering and performance goals once an aircraft is put into operation.ĭuring flight, an aircraft would prefer to encounter laminar flow. The flow regime is important in aircraft design and engineering, as it determines the amount of lift and drag acting on an airfoil. On an aircraft, an airfoil is the structure responsible for moderating lift and drag created by oncoming airflow. Typical laminar-to-turbulent flow transitions over airfoils occur at Reynolds numbers of approximately 500,000.Īir traffic wouldn’t be possible without laminar flow and airfoils. When airflow transitions to turbulent at high Reynolds numbers, the result is greater drag. Both approaches have been applied.Airflow over airfoils generates lift and drag, and the amount of lift depends on the flow regime.
#High lift airfoil code
In the second case is needed to provide the possibility to call CFD code from the optimisation process, and there is no need to build any model, it is being built internally during the optimisation process. In this first case the model is build independent from the optimisation and then use it as a black box in the optimisation process. With MACROS is possible performing either optimisation of the model built with predefined training sample (GSO) or Iterative Surrogate-Based Optimization (SBO). Different metamodeling techniques have been compared based on multiple performance criteria. This work outlines the development of integrated systems to perform aerodynamics multi-objective optimisation for a three-element airfoil test case in high lift configuration, making use of surrogate models available in MACROS Generic Tools, which has been integrated in our design tool. To cut down the cost, surrogate models, also known as metamodels, are constructed from and then used in place of the actual simulation models. Despite advances in computer capacity, the enormous computational cost of running complex engineering simulations makes it impractical to rely exclusively on simulation for the purpose of design optimisation. The ability of the calculation method to accurately predict changes in objective function value when gaps, overlaps and element deflections are varied is therefore critical. The ultimate goal of an aircraft high lift system design team is to define the simplest configuration which, for prescribed constraints, will meet the take-off, climb, and landing requirements usually expressed in terms of maximum L/D and/or maximum CL.
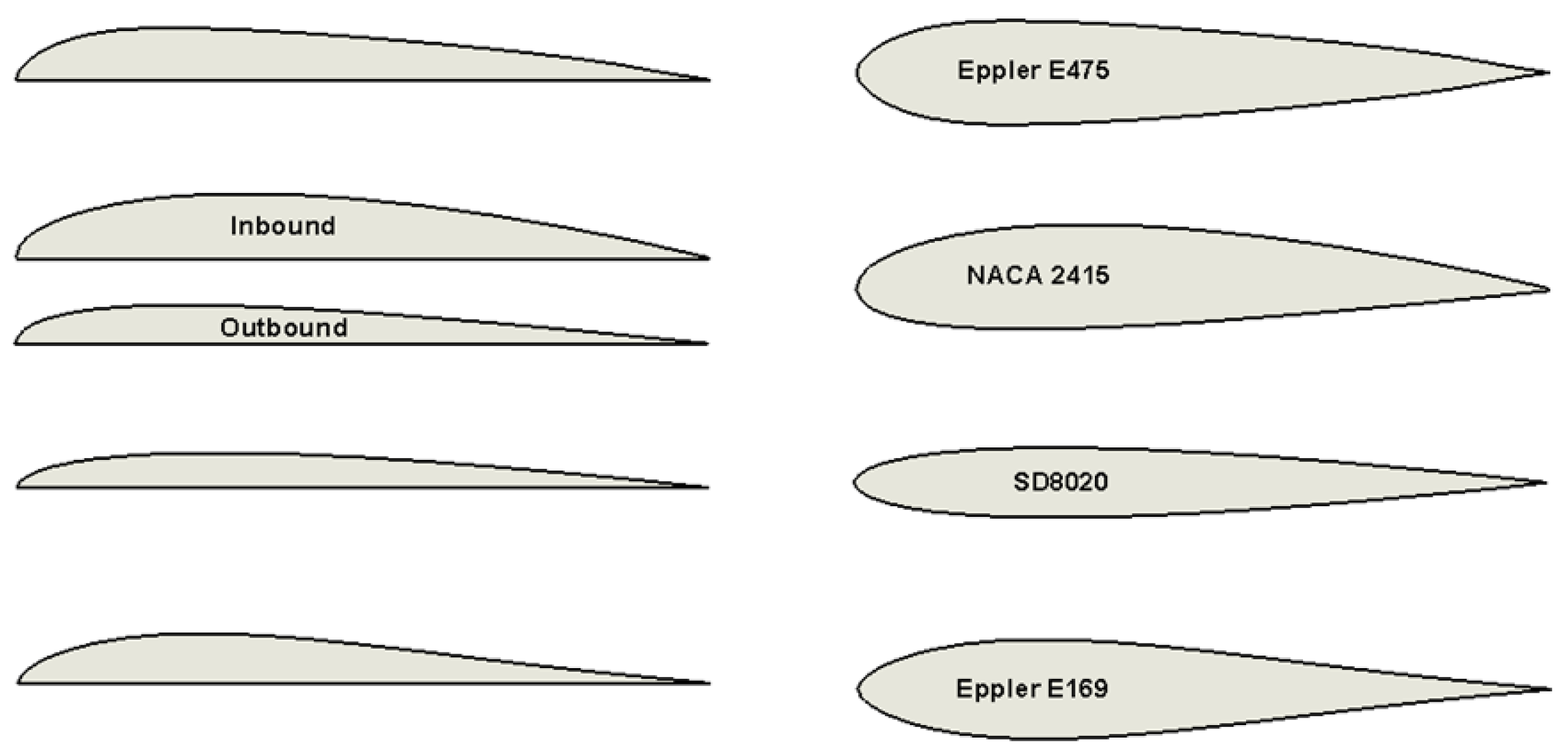

Although the high-lift system is applied only during take-off and landing in the low speed phase of the flight the cost efficiency of the airplane is strongly influenced by it. This work deals with the aerodynamics optimisation of a generic two-dimensional three element high-lift configuration.
